
So, a quadrature encoder with a resolution of 100 pulses per revolution would actually produce 400 different states for each revolution of the encoder. This timing diagram comes directly from an insert that ships with an encoder: This results in 4 different “states” (see a, b, c, and d in the picture below) that the combination of the outputs could be in for any given disc position. The “A” and “B” slots on the encoder disc are offset so that their outputs are out of phase by 90 degrees. These different sets of slots are referred to as channels and are typically called “A” and “B”. Quadrature encoders utilize two different sets of “slots” on the optical disc inside the case. Quadrature EncodersĪll encoders from AutomationDirect are also quadrature encoders. Capacitive technology alsoĪllows the ability to digitally set the index pulse and alignment of the encoder for BLDC commutation, while its built-in diagnostic capabilities provide designers access to valuable system data for quick troubleshooting in the field. Resolutions available in capacitive encoders are not only useful for system optimization, particularly when designing for PID control loop, but can reduce inventory levels, as one model can be used across multiple applications. Given their digital nature, capacitive encoders also offer increased flexibility, allowing users to change the encoder’s resolution while a typical optical or magnetic encoder must be swapped out each time a different resolution is needed. Immune to magnetic interference and electrical noise, it is as rugged as a magnetic encoder but delivers greater accuracy and higher resolution. Further, with no LED, it has a longer lifetime, a smaller footprint, and lower current consumption (6 to 18 mA) than an optical encoder. Capacitive encoders are very rugged, tolerating a range of environmental contaminants such as dust, dirt, and oil, as well as vibration and temperature extremes. The receiver detects the changes in capacitance-reactance on the receiver board and translates these changes, using a demodulation algorithm, into increments of rotary motion.ĭerived from the same principles used in digital calipers, capacitive encoders are highly reliable and accurate. The rotor contains a sinusoidal pattern and, as it rotates, the high-frequency reference signal of the transmitter is modulated in a predictable way. The Modular Kit Encoders (from CUI Devices) sold by AutomationDirect are capacitive encoders intended primarily for use with our stepper motors and to commutate BLDC motors.Ī capacitive encoder is comprised of three main components: a rotor, a stationary transmitter, and a stationary receiver. As the slots pass between the emitter and receiver, the receiver alternately detects light and dark this is how the encoder senses movement and measures position. An emitter on one side of the disc emits light through the slots to a receiver on the other. A 1000 PPR encoder has 1000 slots cut into the disc. The number of slots in the disc varies depending on the resolution of the encoder. Optical encoders contain a disc within the case with “slots” or “lines” cut into it. Optical EncodersĪll of the Koyo encoders sold by AutomationDirect are optical rotary encoders. All the encoders sold by AutomationDirect are rotary encoders. A 2000 PPR encoder has twice the resolution of a 1000 PPR encoder. Rotary encoder resolution is measured in pulses per revolution (PPR), also known as “line count”.

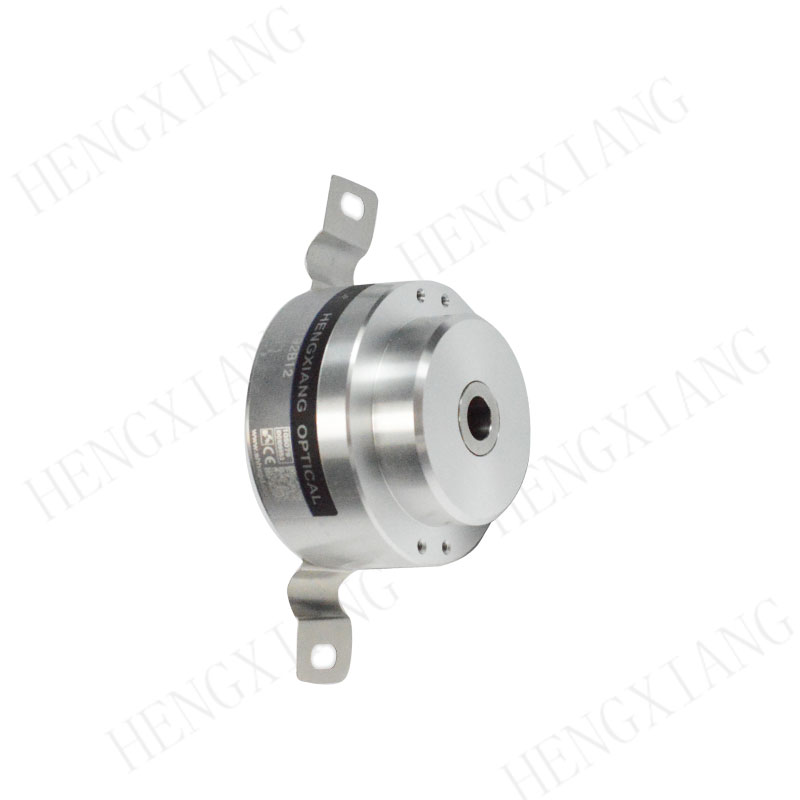
The scale (coded strip) has a set resolution embedded into it or on it that the head reads. A linear encoder’s resolution is measured in pulses per distance (pulses per inch, pulses per mm, etc.). Rotary and linear encoders both define their accuracies in similar ways.
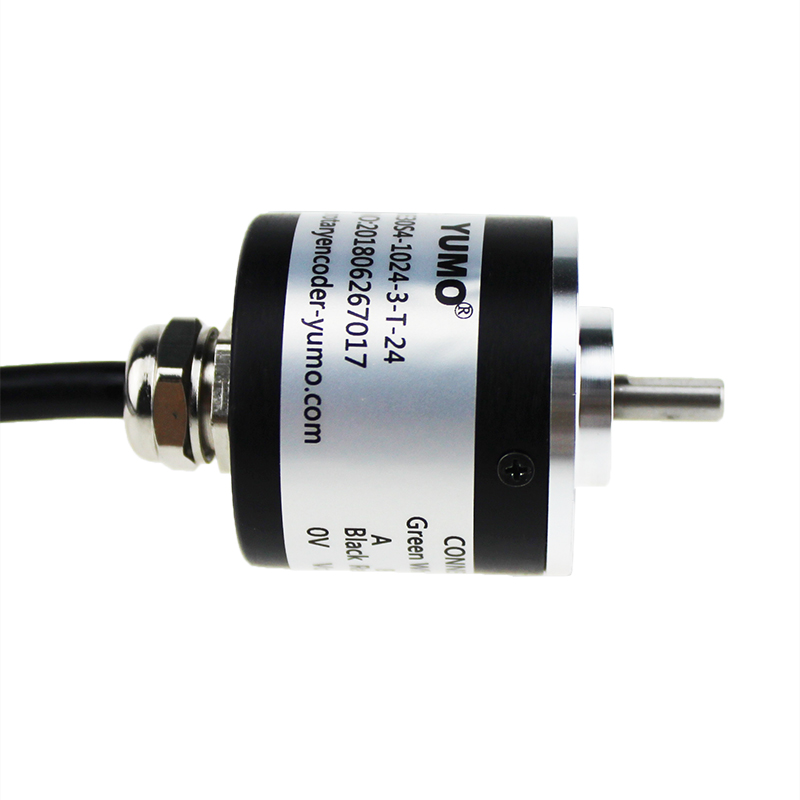
A linear encoder is very similar to a tape measure, while a rotary encoder is more like a measuring wheel. A rotary encoder typically consists of an internal coded disc and a sensing head to determine rotary position. A linear encoder typically consists of a scale (a coded strip) and a sensing “head” that reads the spacing between the scales’ coding to determine position. There are two basic geometries for encoders: linear and rotary. The position information can be read in many ways (optically, magnetically, capacitively, etc.). An encoder (for industrial controls) is a special sensor that captures position information and relays that data to other devices.
